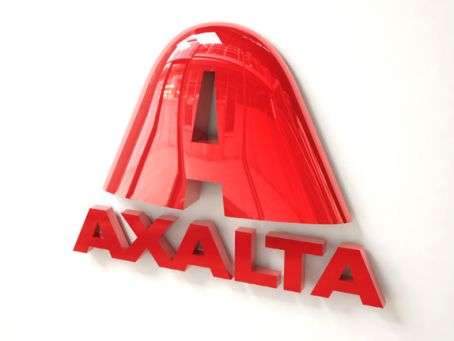
«Однако задача по поддержанию и улучшению продолжает развиваться, открывая новые возможности для компаний по производству покрытий, способных внедрять инновации», - добавил он.
«Axalta празднует свой 150-й год в сфере производства покрытий, и некоторые из этих ожиданий не изменились за столько лет. Для OEM-производителей основными требованиями являются доступность продукта, постоянное качество продукта, соответствующее спецификациям, и обслуживание мирового класса - все это предлагается по конкурентоспособной цене.
Это ожидание справедливо везде, где клиент производит автомобили. Владельцы автомобилей, однако, ищут длительную красоту и легкое обслуживание.
«Хотя 150 лет - это то, чем можно гордиться, вместе с нашими клиентами мы продолжаем смотреть в будущее. Для Axalta это означает сосредоточиться на постоянном улучшении нашего текущего ассортимента продукции и прогнозировании будущих потребностей в покрытиях, будь то регулирование, изменение ожиданий потребителей или постоянное развитие архитектуры автомобилей, которая сопровождается новыми технологиями », - заключил Маркевич.
Усилия Axalta в области исследований и разработок соответствуют потребностям, желаниям и тенденциям клиентов. Маркевич сказал, что компания специально удовлетворяет потребности, предъявляемые новыми материалами, включая мультиметаллы и новые подложки; необходимо повысить производительность и снизить стоимость применения наших систем покрытия; и способы привнести инновационные цвета и эффекты для удовлетворения интересов потребителей в меняющихся тенденциях.
Туми из BASF сказал, что требования к качеству покрытия клиентов относительно просты. «Наши клиенты хотят получить надежное качество, великолепные цвета, отличную отделку автомобиля, и производство на линии будет очень эффективным», - сказал он.
Он добавил: «BASF продолжает уделять особое внимание творческому цветовому дизайну, послойному продвижению продукции, надежности, качеству, эффективности и производительности. Наше электронное пальто Cathoguard 800 - самое эффективное и наиболее эффективное к-пальто на рынке. И не забывайте, BASF впервые внедрил интегрированный процесс, чтобы помочь нашим клиентам повысить их эффективность. Мы по-прежнему стремимся быть лидером отрасли в области новых технологий».
Доктор Клеменс Бартманн, глобальный директор по технологиям OEM для систем покрытия Axalta. Благодаря сильному движению в сторону устойчивости, дизайн кузова автомобиля претерпевает радикальные изменения. В ответ на это компания Axalta Coating Systems искала способы решения проблем, с которыми сталкиваются эти новые легкие материалы. Все большее давление со стороны регулирующих органов оказывается на автомобильную промышленность с целью продвижения к более устойчивым материалам и процессам.
В течение нескольких десятилетий нормативные требования, такие как сокращение выбросов органических растворителей, общее сокращение выбросов CO2 и повышение эффективности использования топлива, побудили индустрию покрытий разрабатывать новые, экологически устойчивые покрытия, такие как материалы с высоким содержанием твердых частиц или воды и консолидированные системы, такие как без грунтовки, двухмокрые или трехмокрые системы.
Чтобы снизить общий вес кузова, производители оборудования хотят увеличить использование материалов меньшего веса, включая алюминиевые, магниевые и полимерные подложки.
Процессы окраски и материалы должны быть соответствующим образом адаптированы. В случае полимерных подложек температуры обжига для процессов отверждения покрытия должны быть снижены.
Легкие материалы помогают сократить выбросы CO2 в лакокрасочном цехе, так как энергопотребление может быть уменьшено при использовании материалов для выпечки. Эти материалы также предлагают расширенные возможности моделирования благодаря новым возможностям в части и геометрии автомобиля. Возможность он-лайн и поточного покрытия кузова и пластиковых деталей означает, что есть возможность улучшить цветовую гармонию и упростить цепочку поставок.
Тем не менее, эти легкие субстраты будут создавать проблемы, когда дело доходит до технологий нанесения покрытий. Например, необходимо разработать новые процессы адгезии, которые могут повлиять на выпекание клеев и покрытий.
Долговременная долговечность и возможность повторного покрытия систем с более низким выпеканием также должны быть обеспечены.
Общий вид окончательной отделки, которая может охватывать различные подложки и линии, должен быть согласован.
Тем не менее, уже существуют некоторые решения для покрытий с низким выпеканием. Они включают в себя хорошо отработанные процессы с множеством технологий и субстратов, используемых для: автомобильных пластиковых деталей, тяжелых грузовиков, которые требуют все более требовательного внешнего вида и высокого уровня качества от грунтовок и верхних слоев с низким уровнем выпекания, и специализированных OEM-производителей, где системы смешивания с низким выпеканием обеспечивают небольшие партии специфических для клиента "цветов галстука".
Тем не менее, дополнительные решения и процессы все еще необходимы для решения проблем, связанных с недавно созданным, разнообразным набором субстратов.
Этого можно избежать, установив ультрафиолетовые лампы на роботов, которые могут достичь всех областей и обеспечить надлежащее отверждение. Это решение может быть использовано в сочетании с водной системой с тремя слоями влаги или без грунтовки, что дает возможность уменьшить общую длину печи с прозрачным лаком до 70 процентов.
Другие технологии сшивания, такие как 2K эпоксидная кислота, 2K акрил / меламин с разблокированным катализатором или 1K акрил / меламин с блокированным катализатором, могут снизить температуру прокаливания близко к заданному значению, но могут иметь другие проблемы, такие как стабильность или технологические свойства с эти условия отверждения.
До сих пор ведущей технологией сшивки для покрытий с низким содержанием обжига являются полиуретаны 2K.
Другой вариант - химический состав (поли) аспартата, доступный через прямую процедуру синтеза.
Он показывает многообещающие результаты в достижении очень хороших технологических свойств, таких как долговечность и химическая стойкость, даже при температуре отверждения при комнатной температуре благодаря очень быстрой реакции сшивания.
Это также дает возможность составлять покрытия с более высоким содержанием твердых частиц, чтобы сочетать преимущества более низкого выпекания и более низких выбросов растворителя. И последнее, но не менее важное: существует еще одна проблема, связанная с опусканием окна отверждения для электроосаждения покрытия, поскольку в будущем в конструкции кузова все еще будут присутствовать значительные металлические компоненты.
Путь к снижению обжига ED покрытий может быть описан в три этапа развития.
Первый - это целевая выпечка T max на внешней стороне при 180 ° C, что будет означать минимальные требуемые температуры 165 ° C -170 ° C.
Это может способствовать снижению энергопотребления в малярном цехе. Axalta добилась положительных результатов благодаря современной коммерчески доступной технологии Aqua EC4027, благодаря которой она достигла хорошей стойкости к растворителям и коррозии до 10 минут при 150 ° C.
На следующем этапе разработки может быть достигнут температурный интервал (T max = 140 ° C), позволяющий оперативно наносить покрытие на конкретные пластмассовые детали - иными словами, металлические и пластмассовые пасты могут проходить через ванну ED и покрываться сверху.
Здесь есть потребность в новой химии сшивания и значительном развитии процесса и материалов. Также необходимо решить вопрос о повышении температуры для выпекания закалочной стали.
Необходимо доказать потенциальные преимущества дальнейшего снижения температуры обжига ED, например, до 80-125 ° C - однако это будет более длительный процесс разработки.
Следующим важным шагом будет дальнейшая интеграция отдельных решений - материалов, процессов и приложений - в реальных средах массового производства.
Для нанесения металликов, а также лаков мы предлагаем использовать краскораспылители Devilbiss GTIPRO Lite.